In fast-paced manufacturing environment, the demand for effectiveness and speed has never been greater. Companies are constantly seeking innovative solutions to reduce lead times and lower production costs without sacrificing quality. One such innovation revolutionizing the industry is rapid injection molding. This cutting-edge technique is transforming the way products are manufactured, enabling businesses to bring their ideas to life in record time.
Rapid injection molding bridges the gap between traditional molding methods and the immediate need for quick prototyping and production runs. By leveraging advanced technologies and materials, manufacturers can create high-quality components much faster than ever before. This process not only optimizes the entire production cycle but also allows for greater design flexibility, making it an essential tool for businesses that aim to stay competitive in a challenging market.
Benefits of Accelerated Injectable Forming
Rapid injectable molding offers substantial advantages that simplify the product manufacturing process. One of the main advantages is the pace of production. Conventional injection forming can take several weeks or even a couple of months for setup. In contrast, accelerated injection molding dramatically cuts down this period, allowing for faster prototyping and quicker industry introduction. Companies can acquire functional parts in a timeframe of a few days, improving their ability to react to customer demands and consumer feedback.
Another key advantage is cost-effectiveness. Rapid injectable forming uses advanced technologies and resources that lower the total cost of production, particularly for small to moderate volume batches. The shortened turnaround times and reduced waste add to cost savings, enabling businesses to allocate resources more efficiently. Moreover, with the ability to make changes quickly during the development phase, manufacturers can prevent expensive mistakes that typically occur in traditional molding processes.
Additionally, the creative flexibility provided by accelerated injectable molding is unmatched. Manufacturers can experiment with various materials and styles without the economic burden of traditional molds. This flexibility encourages creativity and personalization, enabling companies to adapt products to specific customer needs or preferences. By promoting creativity and adaptability, accelerated injectable molding not only enhances product standards but also strengthens a brand's competitive edge in the industry.
Uses in Various Industries
Fast injection molding has carved its place across multiple sectors, greatly improving the speed and effectiveness of goods manufacturing. In the car industry, for example, fast injection molding facilitates the quick production of components such as dashboard parts, trims, and casings. The ability to create prototypes swiftly allows manufacturers to evaluate designs and make necessary adjustments before going into large-scale production, thereby reducing the time it takes to reach the market for innovative vehicles.
In the consumer products industry, rapid injection molding empowers companies to create and enhance everyday items like cooking utensils, electrical housings, and personal care products. The process enables brands to react quickly to market changes and consumer preferences. As businesses strive to provide innovative solutions, fast injection molding streamlines the process from concept to commercialization, giving companies a market advantage in a fast-paced marketplace.
The healthcare industry also benefits immensely from rapid injection molding , especially in the manufacturing of exact components for medical equipment and tools. Custom tools, casings, and connectors can be produced in a fraction of the time traditionally needed, permitting for faster advancements in healthcare technology. This ability to react quickly not only enhances patient care but also facilitates regulatory adherence by allowing faster revisions of design testing and validation.
Upcoming Trends in Manufacturing
The landscape of manufacturing is regularly evolving, and swift injection molding is at the cutting edge of this transformation. As industries increasingly require quicker turnaround times and greater flexibility in production, the integration of advanced techniques such as artificial intelligence and machine learning into swift injection molding will become more prevalent. These technologies will enhance the design and production processes, allowing manufacturers to review data in real-time, modify to market needs quickly, and enhance decision-making.
Green initiatives is another critical trend shaping the future of manufacturing. Companies are now focusing on sustainable practices and materials, pushing the boundaries of rapid injection molding to include compostable plastics and recyclable options. This transition not only satisfies consumer desires for greener products but also aligns with regulatory requirements across diverse industries. As a result, manufacturers are putting resources in researching sustainable materials that will still provide the performance and caliber expected from traditional injection molded products.
Lastly, the increase of tailoring is transforming the manufacturing sector. As consumer tastes evolve toward tailored products, fast injection molding offers a solution that merges speed with tailoring capabilities. Manufacturers can quickly modify designs and produce miniature batches cost-effectively, thus catering to specific customer needs without compromising efficiency. This trend will reshape product development cycles, allowing businesses to keep agile in a market that increasingly cherishes individuality and tailored solutions.
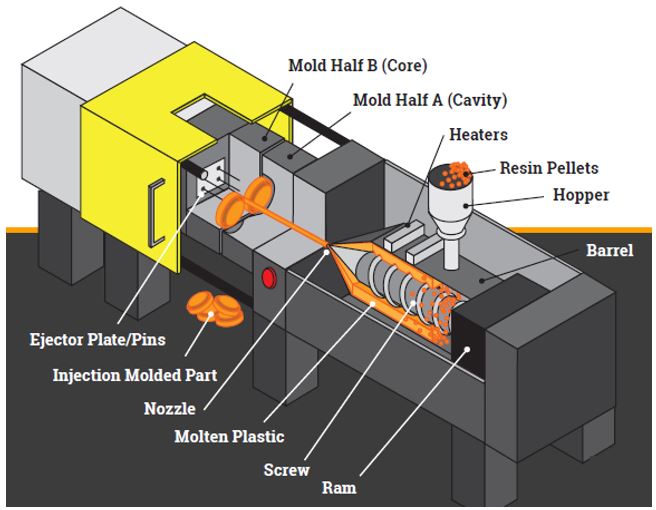